Ensuring Reliability: The Importance of Diesel Fuel Testing and Polishing for Backup Generators
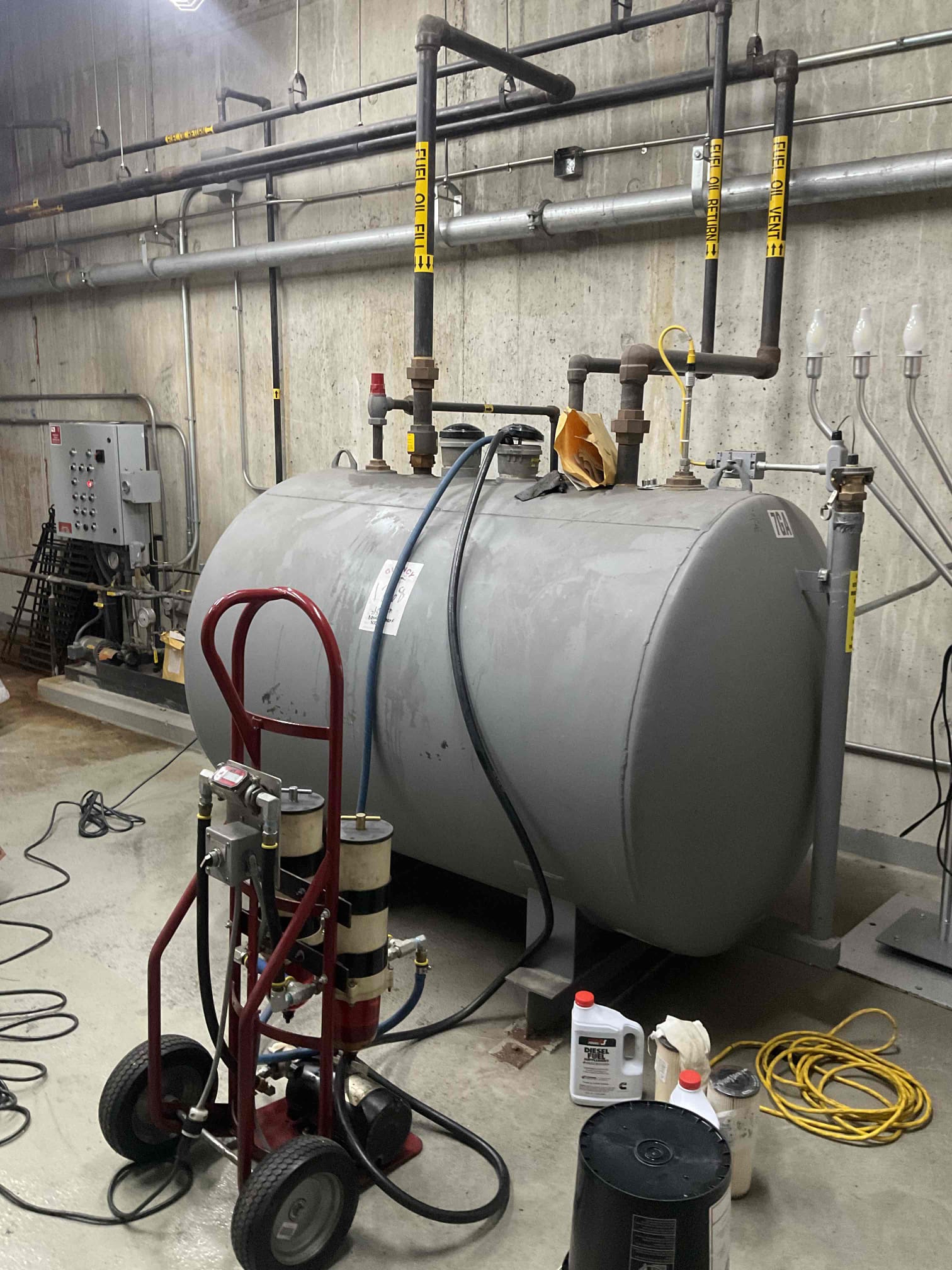
Backup generators are a crucial lifeline for many organizations, providing a reliable power source during unexpected outages. Whether it’s a hospital, data center, or critical infrastructure facility, the reliability of backup generators is paramount. However, the effectiveness and longevity of these generators heavily depend on the quality of the diesel fuel they run on. This is where diesel fuel testing and diesel fuel polishing come into play. These practices are essential for ensuring that backup generators provide an uninterrupted power supply.
Table of Contents
What is Diesel Fuel Testing?

Diesel fuel testing involves the analysis of fuel samples to determine their quality and suitability for use. Key parameters checked during testing include:
- Water Content: Water in diesel fuel can cause microbial growth, corrosion, and poor combustion.
- Particulate Matter: Solid contaminants can clog filters and damage engine components.
- Microbial Contamination: Bacteria and fungi can grow in diesel fuel, especially in the presence of water, leading to sludge formation and filter blockages.
- Cetane Number: Indicates the combustion quality of the diesel fuel. Higher cetane numbers typically mean better engine performance.
- Sulfur Content: High sulfur levels can lead to harmful emissions and engine deposits.
Why is Diesel Fuel Testing Important for Backup Generators?
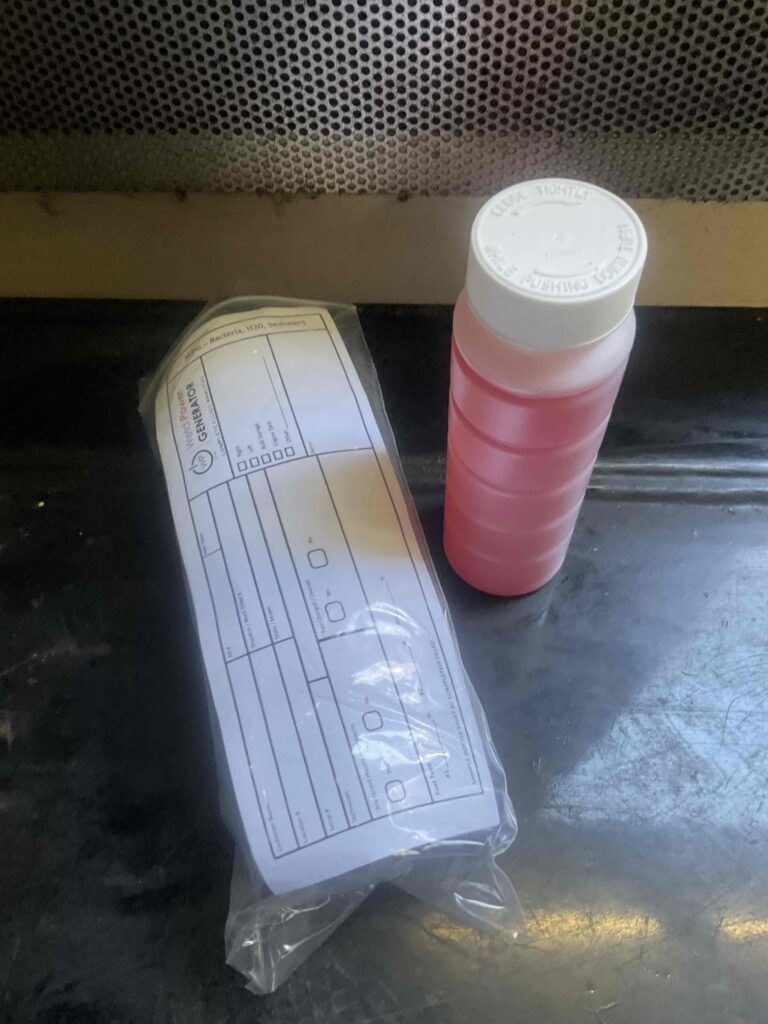
Diesel fuel typically starts to degrade within 6 to 12 months of storage if not properly treated or maintained. Factors such as exposure to air, water contamination, temperature fluctuations, and microbial growth can accelerate this process, leading to reduced fuel quality and potential engine issues.
- Ensuring Engine Performance: High-quality diesel fuel ensures optimal engine performance, reducing wear and tear and extending the engine’s lifespan.
- Enhancing Fuel Efficiency: Clean fuel burns more efficiently, leading to better fuel economy and reduced operating costs.
- Maintaining Regulatory Compliance: Testing helps ensure that diesel fuel meets environmental and safety regulations, preventing legal issues and fines.
- Preventing Downtime: Detecting contaminants early prevents engine malfunctions and unplanned maintenance, keeping operations running smoothly.
- Protecting Investments: Regular testing safeguards the significant investments made in diesel-powered equipment and infrastructure.
What is Diesel Fuel Polishing?
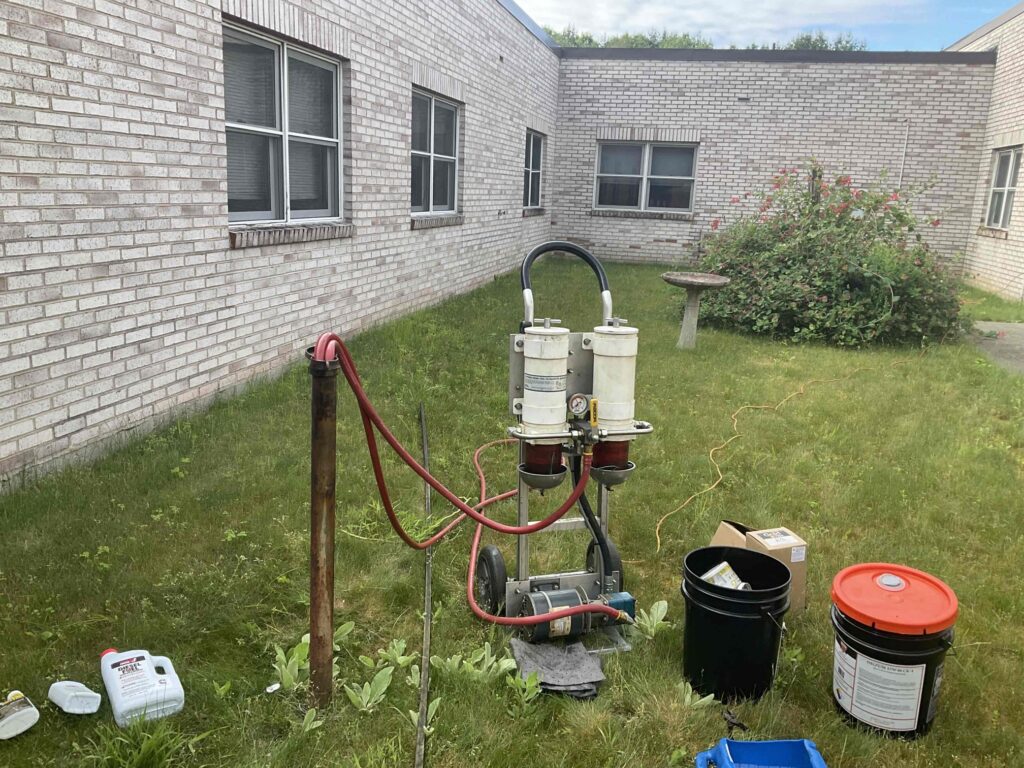
Diesel fuel polishing is the process of cleaning and purifying diesel fuel to remove contaminants such as water, particulates, and microbial growth. It typically involves the following steps:
- Filtration: Removing solid particles through various types of filters.
- Water Separation: Using coalescers and water separators to remove water from the fuel.
- Chemical Treatment: Adding biocides to kill microbial growth and stabilizers to enhance fuel quality.
- Recirculation: Continuously circulating the fuel through the polishing system to ensure thorough cleaning.
Why is Diesel Fuel Polishing Important for Backup Generators?
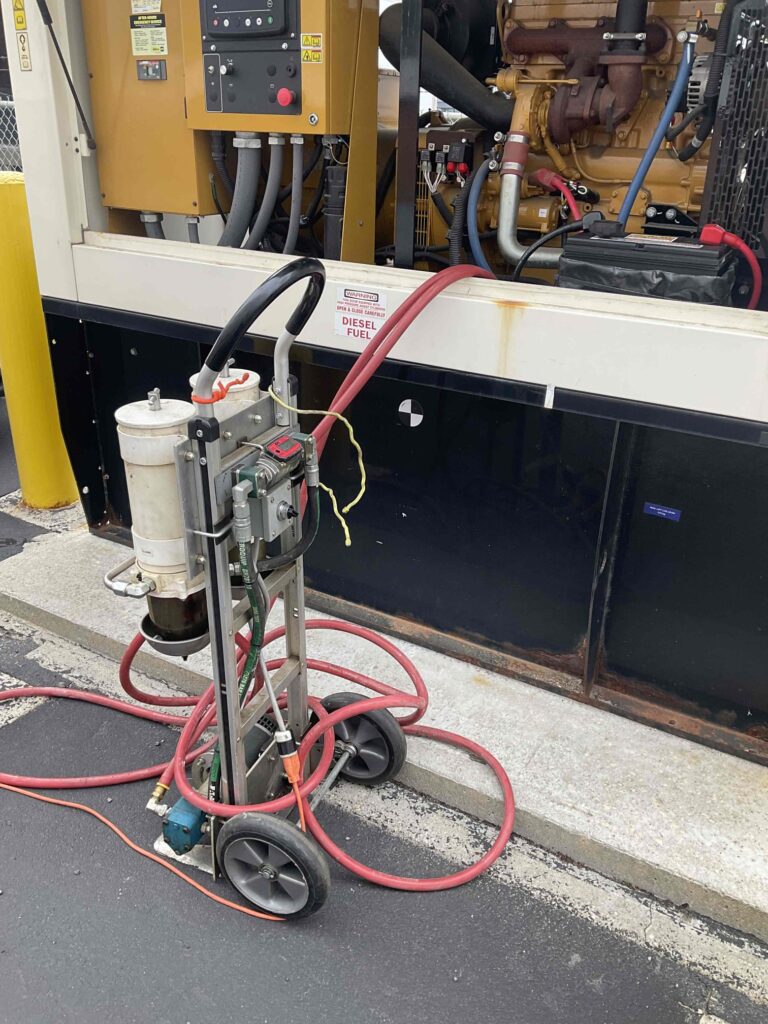
Bad fuel is one of the leading causes of generator failure. Maintaining a quality fuel supply is crucial to ensuring that your backup generator will run when you need it most.
- Improving Fuel Quality: Polishing ensures that the fuel is free from contaminants, leading to better engine performance and longevity.
- Enhancing Reliability: Clean fuel reduces the risk of engine failures and operational interruptions, which is crucial in emergency situations.
- Cost Savings: By extending the life of both the fuel and the engine, polishing can lead to significant cost savings in maintenance and fuel replacement.
- Environmental Protection: Cleaner fuel means fewer harmful emissions, contributing to environmental sustainability.
- Readiness for Use: Polished fuel is always ready for immediate use, which is vital for backup generators in critical applications.
Conclusion
For backup generators, the quality of diesel fuel is a critical factor that directly affects performance, reliability, and operational costs. Diesel fuel testing and diesel fuel polishing are essential practices that ensure the fuel remains clean and efficient, preventing engine issues and extending the reliability generator. By incorporating these practices into a regular maintenance routine, businesses can protect their investments, ensure compliance with regulations, and maintain a reliable power supply.