11 Generator Preventative Maintenance: Key Services, Scope of Work, and Frequency
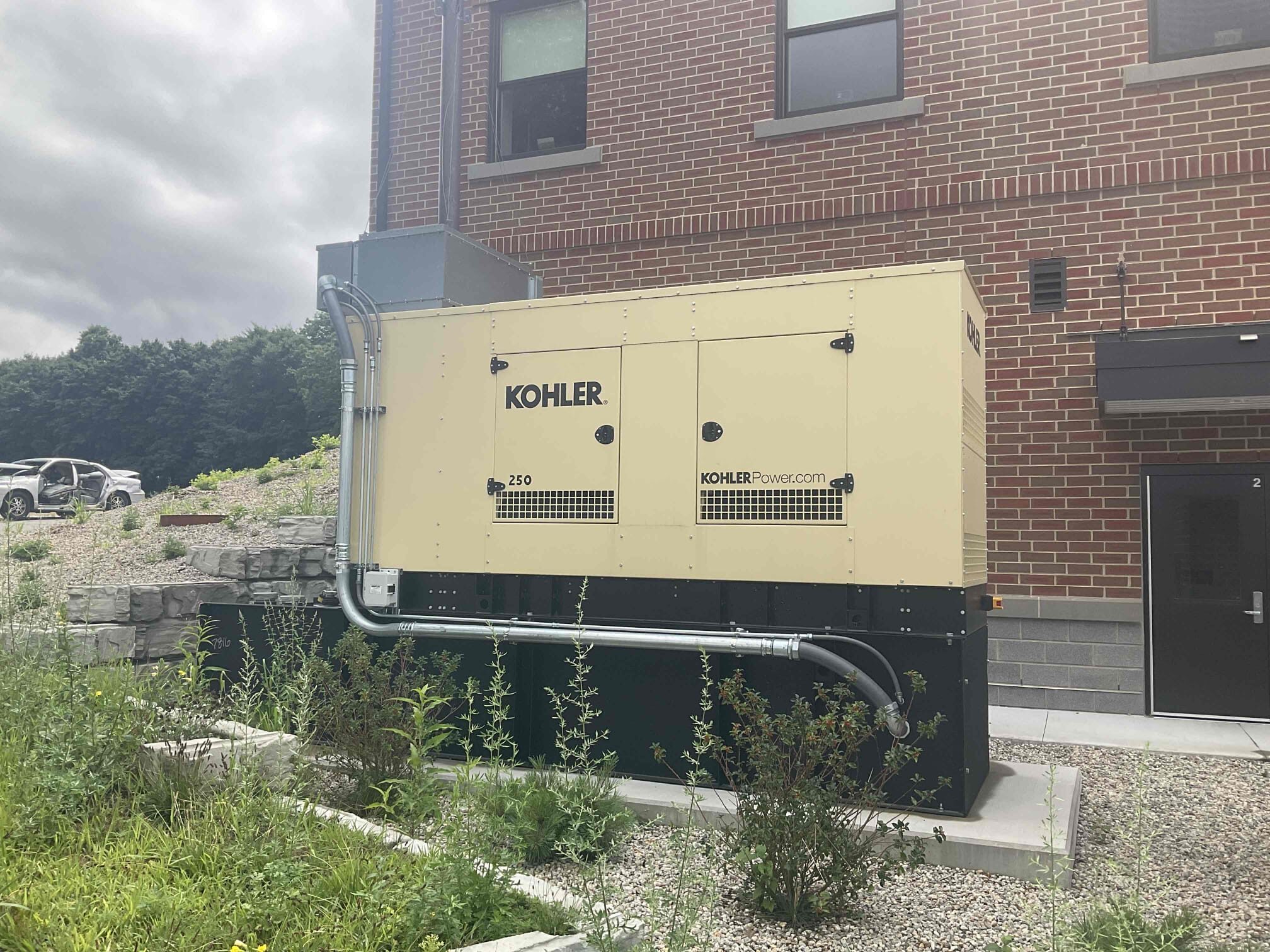
Generator Preventative Maintenance (PM) is essential to ensure that your generator remains reliable, efficient, and ready to provide power when needed. A well-structured maintenance plan not only extends the life of your generator but also prevents costly downtime and repairs. This article will cover the essential aspects of generator preventative maintenance, including Generator Exercise, Minor and Major PMs, Building Load Testing, Load Bank Testing, ATS Maintenance, Oil Sampling, Coolant Sampling, Fuel Sampling, Fuel Polishing, and PM3s. We’ll explore the standard scope of work for each service and the typical frequency.
Table of Contents
Generator Exercise & Visual Inspection
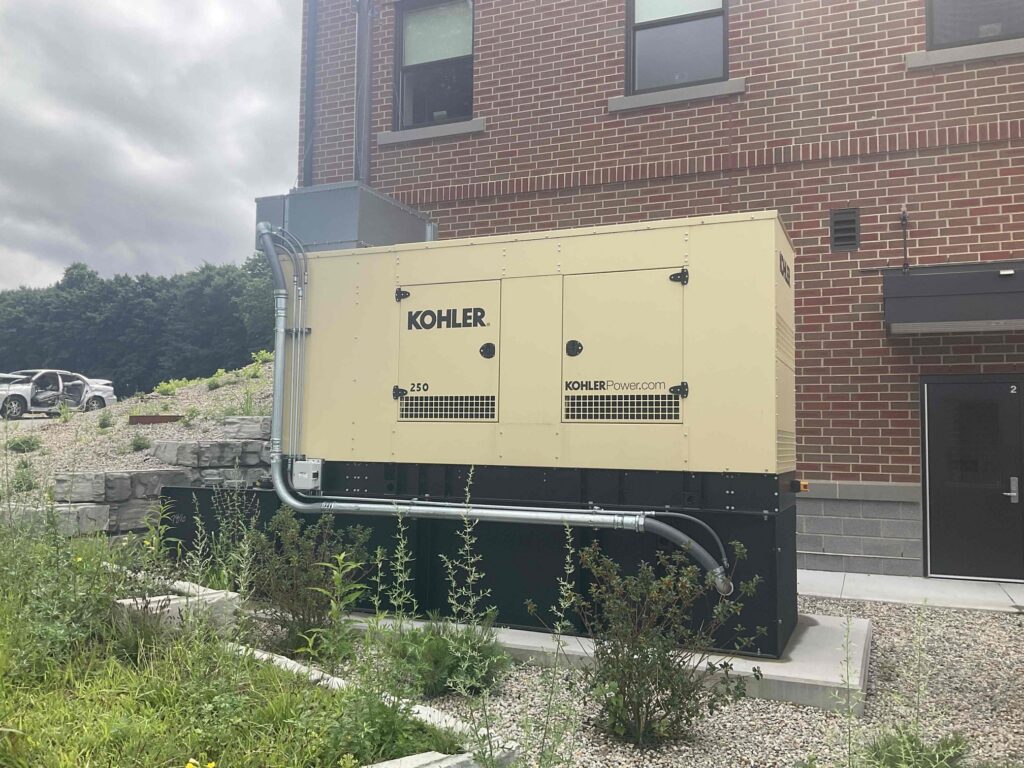
Scope of Work:
Generator exercise involves running the generator under no-load or partial-load conditions to ensure that it is operational. This process helps circulate fluids within the system, lubricate moving parts, and prevent the buildup of moisture and contaminants. It is recommended to have personnel monitor the exercise. During this time, they should look for any obvious leaks, unusual noises, or other signs of potential issues that could indicate a problem with the generator.
Frequency:
- Weekly or Monthly: Depending on the manufacturer’s recommendations and the specific needs of your facility.
- Duration: Typically, exercises last between 20-30 minutes.
Importance:
Regular exercise prevents battery discharge, keeps the engine components lubricated, and helps ensure the generator is ready to handle a load in case of an emergency. Monitoring the exercise allows for the early detection of issues, ensuring that any problems are addressed before they can cause a major failure.
Minor Preventative Maintenance (PM1)
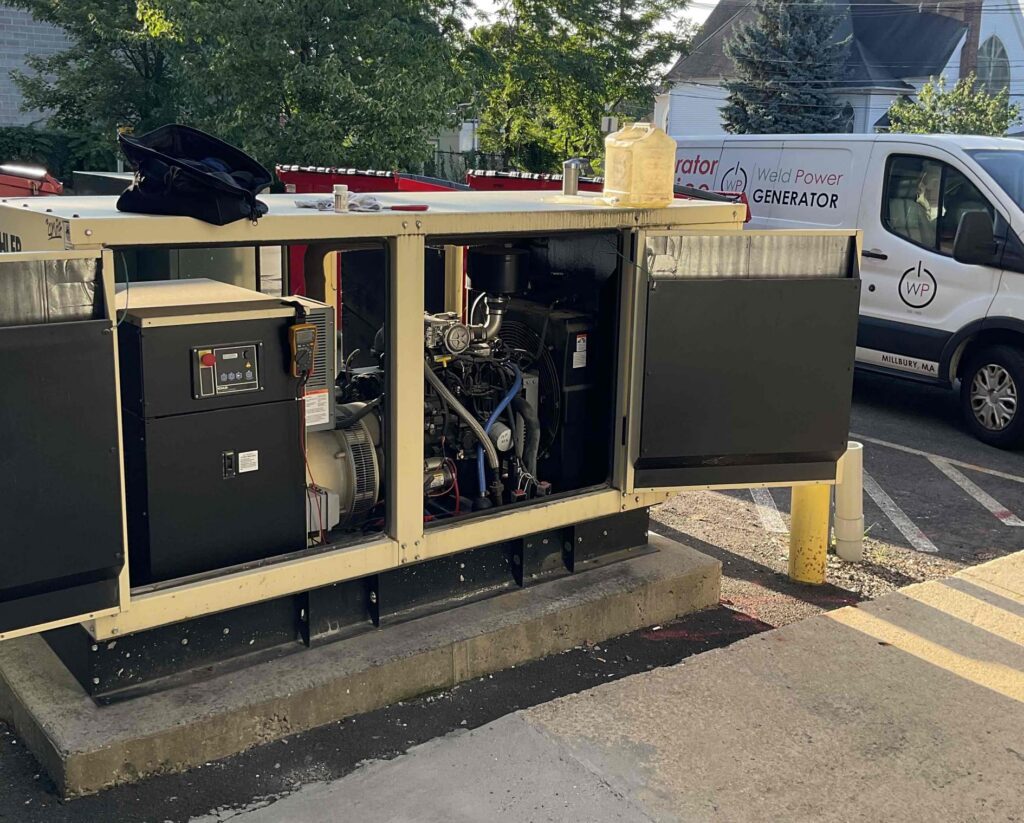
Scope of Work:
Minor PM involves a thorough examination of the generator and its components. Key aspects include:
- Checking fluid levels (oil, coolant, fuel)
- Inspecting belts, hoses, and connections for wear or damage
- Verifying that there are no leaks, corrosion, or other visible issues
- Ensuring the battery is in good condition
- Exercising Generator
Frequency:
- Monthly to Annually: Depending on the usage, environment in which the generator operates, manufacturer recommendations, and criticalness of power.
Importance:
Regular Minor PMs help identify potential issues early, preventing more significant problems and costly repairs down the line.
Major Preventative Maintenance (PM2)
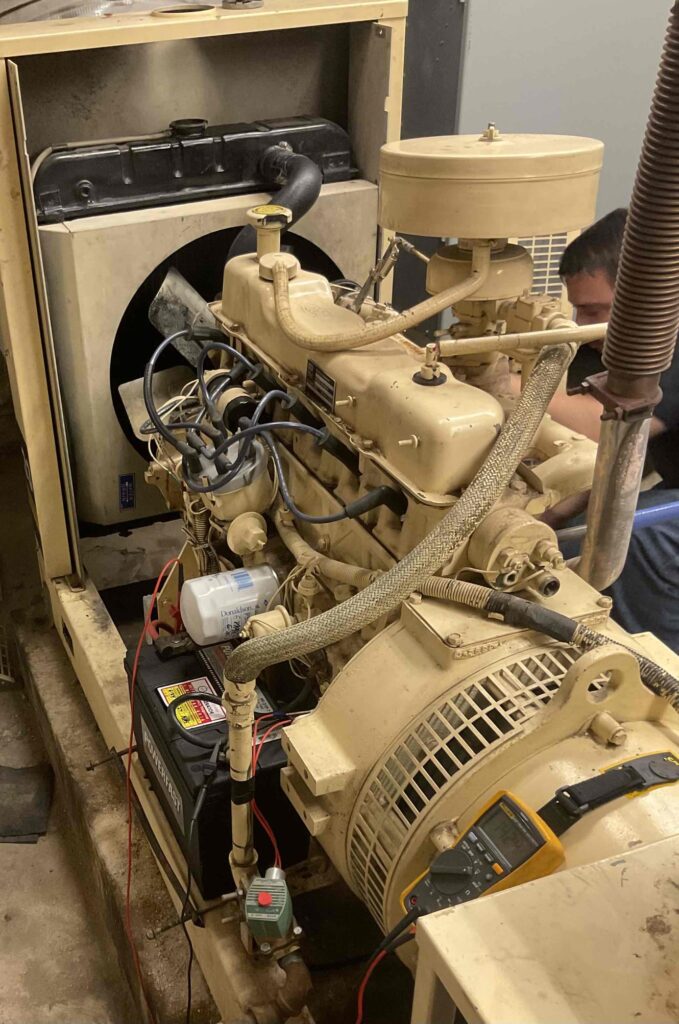
Scope of Work:
Major PM is a comprehensive service that includes detailed inspections and servicing of the generator. Typical tasks include:
- Replacing Oil Filters, Fuel Filters, and Coolant Filters
- Draining and replacing the oil
- Everything included in a Minor PM
Frequency:
- At least Annually: Or as recommended by the manufacturer, typically based on the number of operating hours.
Importance:
Major PM ensures that all critical components are in optimal condition, reducing the risk of failure during operation.
Preventative Maintenance Level 3 (PM3)
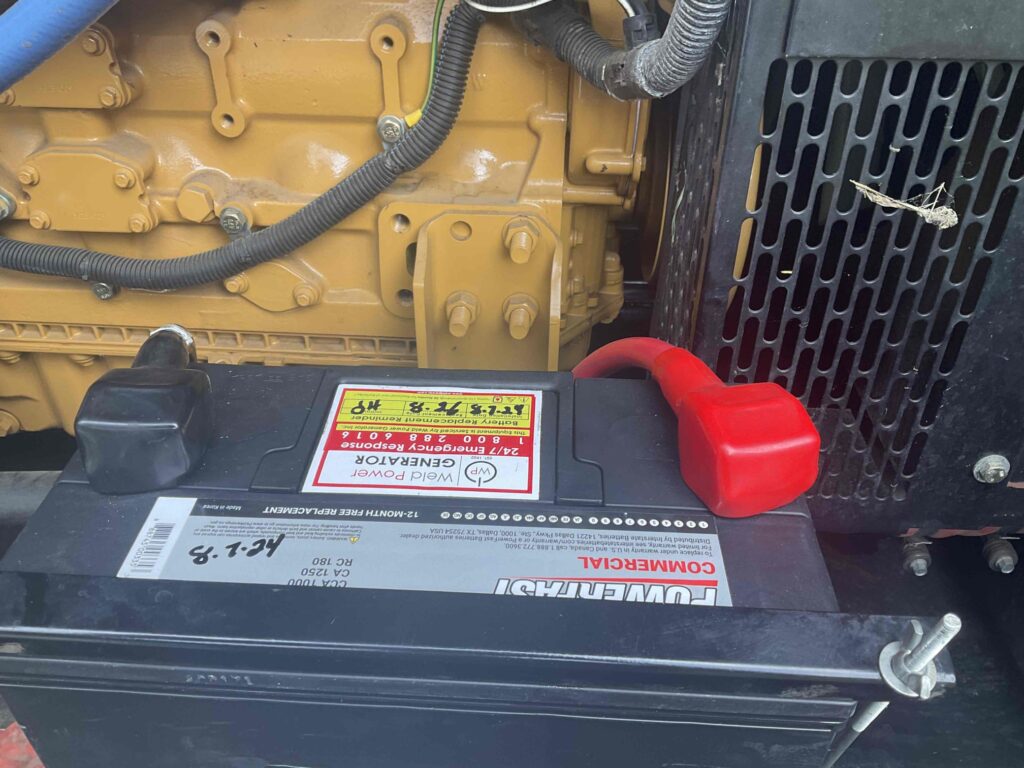
Scope of Work:
PM3, or Preventative Maintenance Level 3, is a comprehensive and in-depth service designed to ensure the long-term reliability and performance of the generator. The scope of work included in a PM3 is usually more customized than the other services on this list, but they typically include:
- Replacing all the belts and hoses
- Replacing the air filter
- Changing the batteries
- Draining and replacing the coolant
- Checking or replacing spark plugs
Frequency:
- Once Every 2-3 Years: Or as recommended by the manufacturer guidelines and NFPA, typically based on the number of operating hours.
Importance:
PM3 is critical for generators that operate under demanding conditions or those that are critical to operations. This level of maintenance goes beyond basic upkeep, addressing wear and tear that may not be immediately visible. By performing PM3 regularly, you ensure that the generator remains in peak condition, extending its lifespan and reducing the likelihood of unexpected failures.
Building Load Testing
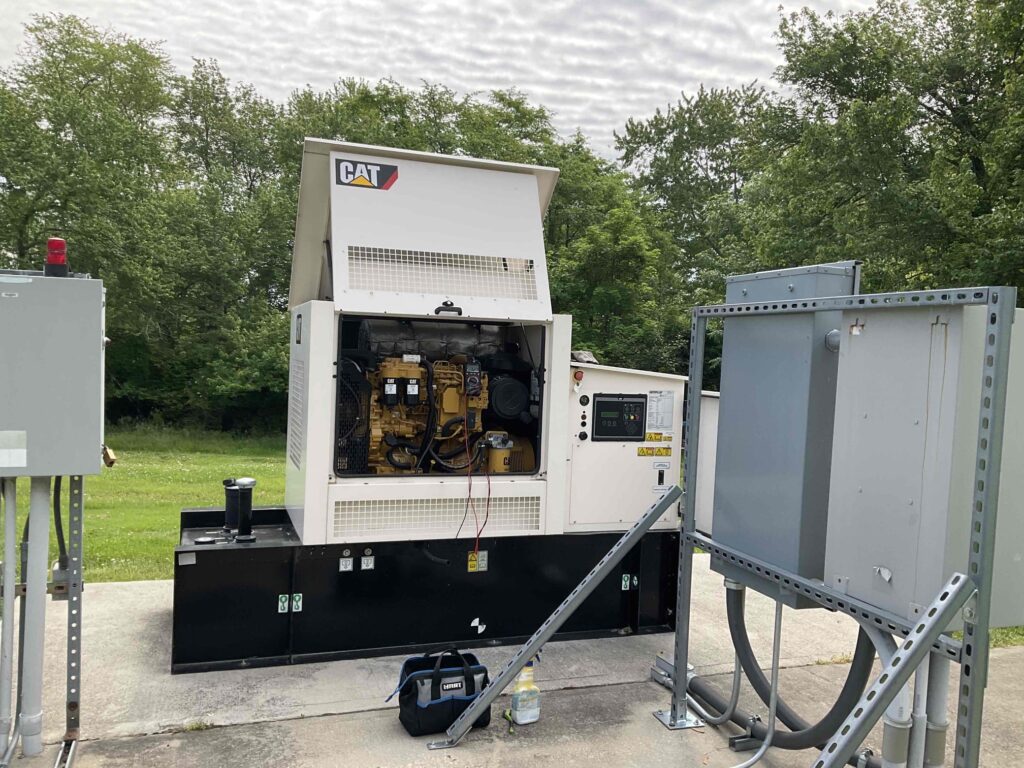
Scope of Work:
Building load testing involves running the generator under the actual load conditions it would encounter during an outage. This test verifies that the generator can handle the building’s electrical load without issues.
Frequency:
- Semi-Annually with Major & Minor: Or after significant changes to the building’s electrical system.
Importance:
Building load testing ensures that the generator can meet the facility’s power demands, preventing surprises during an actual power outage.
Load Bank Testing
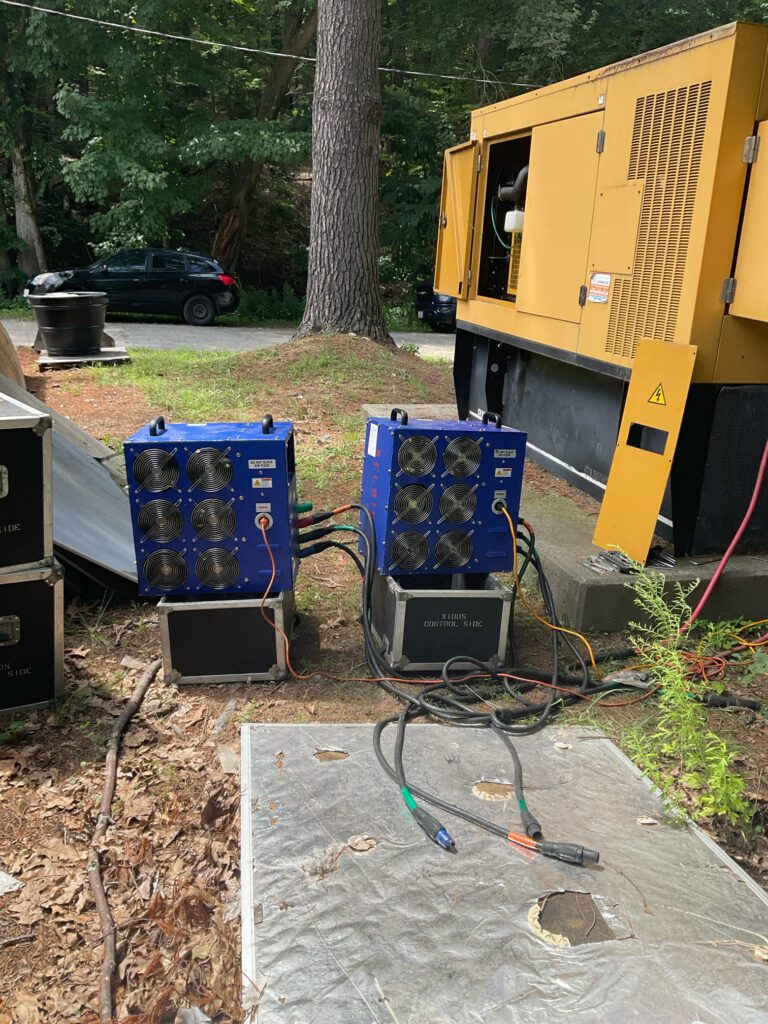
Scope of Work:
Load bank testing is a controlled test where the generator is run at its full-rated capacity. This test helps to:
- Verify the generator’s ability to handle full load
- Burn off unburned fuel (wet stacking) in diesel generators
- Identify performance issues before they lead to failure
Frequency:
- Annually: Recommended for standby generators that are rarely used under full load conditions.
- Duration: Typically, 2 – 4 Hours depending on manufacturer recommendations, NFPA, JCAHO (If applicable), and Criticalness of power.
Importance:
Load bank testing ensures that the generator can perform at its rated capacity when needed, providing peace of mind that it will work during an emergency.
Automatic Transfer Switch (ATS) Maintenance
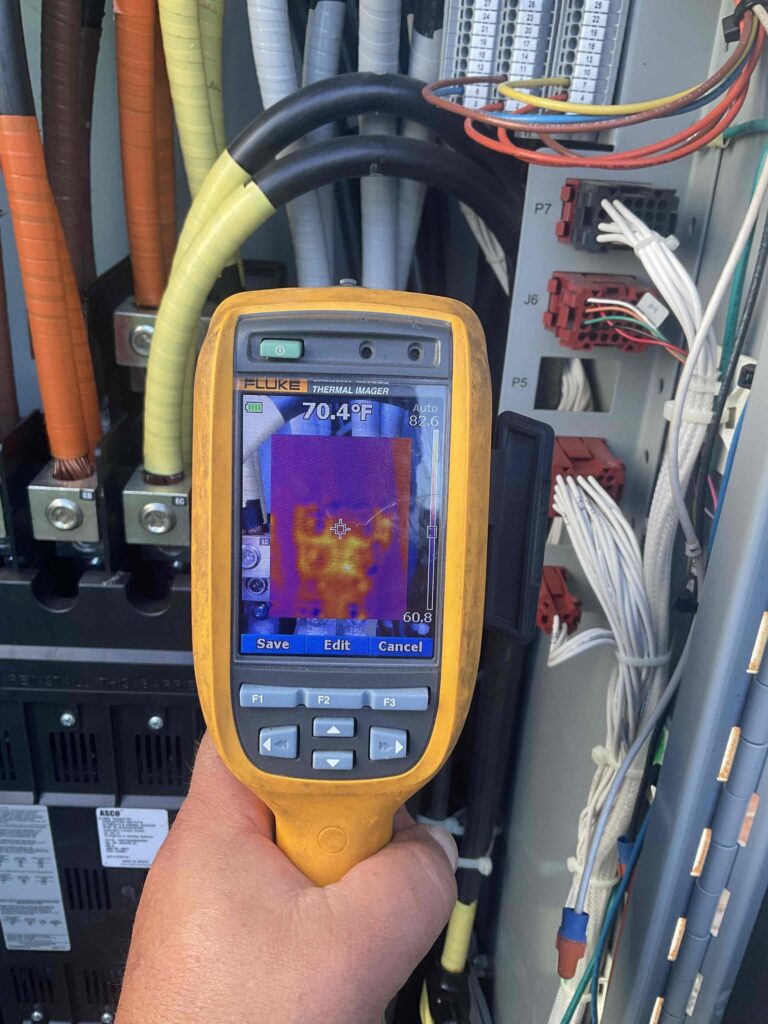
Scope of Work:
ATS maintenance involves inspecting and testing the automatic transfer switch, which transfers the load from the utility to the generator during a power outage. Key tasks include:
- Checking and cleaning electrical contacts
- Testing the switch’s operation and response time
- Verifying the correct configuration of settings
Frequency:
- Annually: Or according to the manufacturer’s recommendations.
Importance:
The ATS is critical to the generator’s operation during an outage. Regular maintenance ensures that it functions correctly, avoiding delays in power restoration.
Oil Sampling
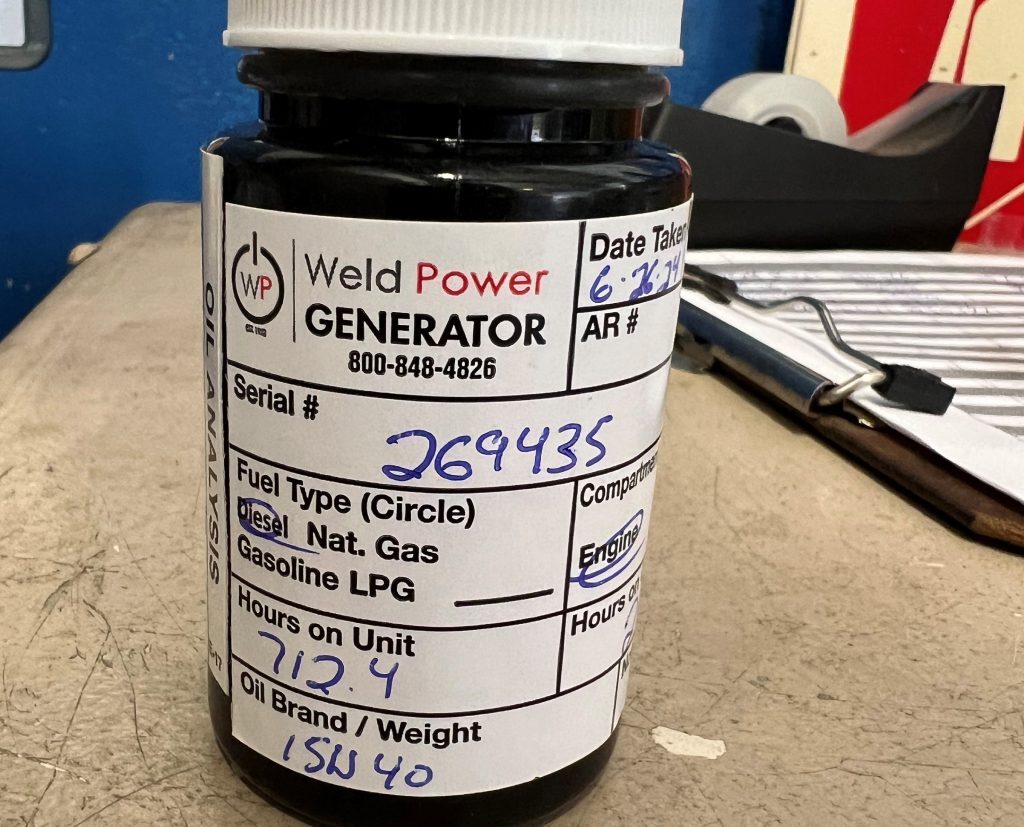
Scope of Work:
Oil sampling involves taking a sample of the generator’s engine oil and analyzing it for contaminants, wear metals, and other indicators of engine health. The analysis provides insights into the engine’s condition and can predict potential failures.
Frequency:
- Annually with Major or Every 250-500 Hours of Operation: Depending on the generator’s usage and the manufacturer’s recommendations.
Importance:
Regular oil sampling helps detect early signs of engine wear, allowing for proactive maintenance and avoiding catastrophic engine failures. This is also crucial for customers that forgo annual oil changes (Extended Drain).
Coolant Sampling
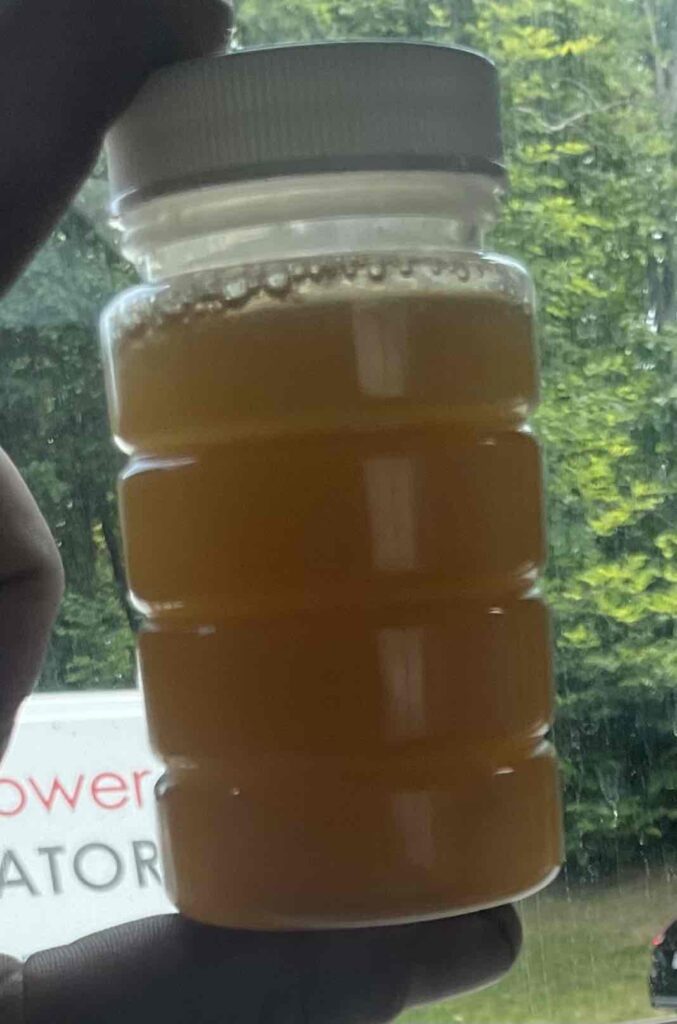
Scope of Work:
Coolant sampling involves testing the generator’s coolant for proper chemical balance, contaminants, and effectiveness. The analysis checks for:
- pH levels
- Presence of contaminants (e.g., oil, fuel)
- Additive levels (e.g., anti-corrosion, anti-freeze)
Frequency:
- Annually with Major: Or more frequently if the generator operates in extreme conditions.
Importance:
Maintaining proper coolant chemistry prevents corrosion, overheating, and other cooling system-related issues, ensuring the generator runs efficiently.
Fuel Sampling (Diesel Generators Only)
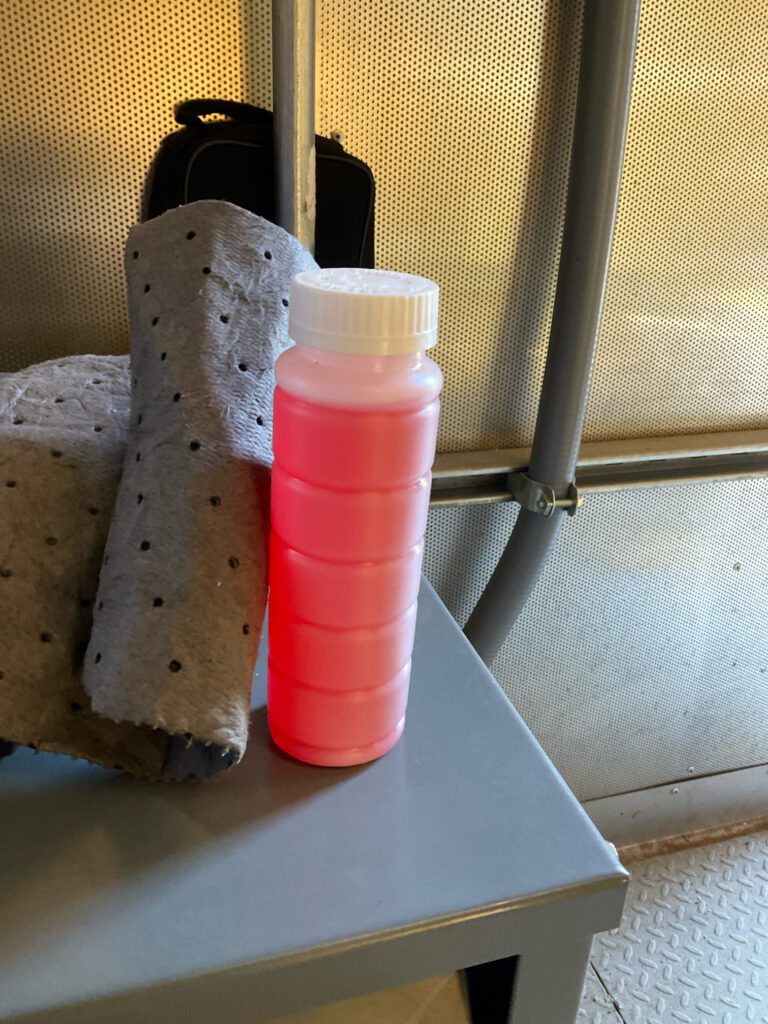
Scope of Work:
Fuel sampling tests the generator’s fuel for contamination, water, and microbial growth. The analysis helps ensure that the fuel is clean and free of impurities that could clog the fuel system or reduce engine performance.
Frequency:
- At Least Annually with Major: Especially for diesel generators that store fuel for extended periods.
Importance:
Clean fuel is essential for reliable generator operation. Contaminated fuel is one of the leading causes of generator failure.
Diesel Fuel Polishing
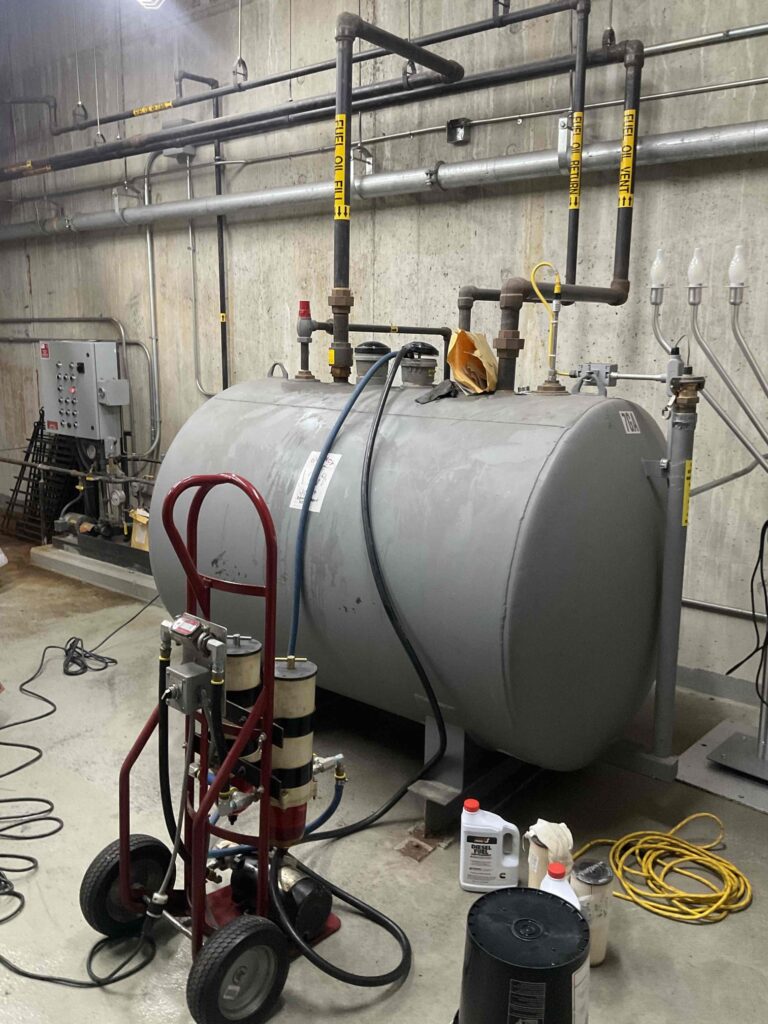
Scope of Work:
Fuel polishing is the process of removing water, sludge, and contaminants from stored fuel. It involves filtering the fuel and treating it with chemical additives to restore its quality.
Frequency:
- Annually or as needed based on fuel samples: especially for diesel fuel stored for long periods.
Importance:
Clean, polished fuel ensures the generator operates efficiently and prevents damage to the fuel system and engine.
Conclusion
Preventative maintenance is a critical component of ensuring your generator is always ready to provide power when needed. Each of the services outlined above plays a vital role in maintaining the health and reliability of your generator. Creating an effective preventative maintenance plan can extend the life of your generator, reduce the risk of unexpected failures, and ensure uninterrupted power for your facility. Investing in a comprehensive maintenance plan is the best way to protect your generator and guarantee its performance during emergencies. Please contact a member of our sales team for a detailed scope of work or sample report for any of these services.