3 Critical Insights You Gain from Fluid Testing in Generator Maintenance Plan
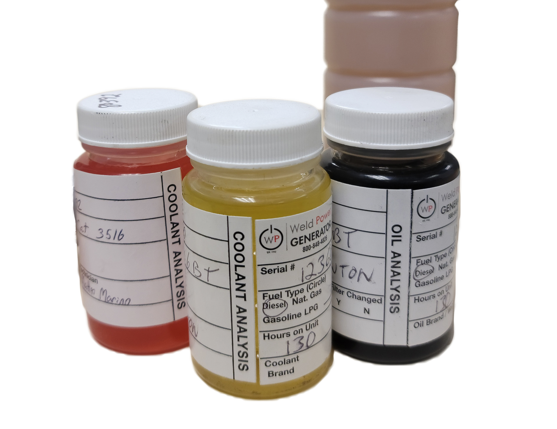
Table of Contents
The Critical Role of Fluid Testing in Generator Preventative Maintenance
Oil, coolant, and diesel fuel testing starts with a technician extracting a sample of the fluids from the generator. From there the samples are sent to a laboratory for testing. In the lab, oil is tested for contaminants, viscosity, and oxidation; coolant for pH, contaminants, and additive levels; and diesel fuel for water content, microbial growth, and stability. The lab will provide a detailed report for each fluid sample. The results can reveal wear and tear, contamination, and fluid degradation, informing necessary maintenance actions. This testing is crucial for preventing engine issues, optimizing performance, and ensuring the generator’s reliability and longevity.
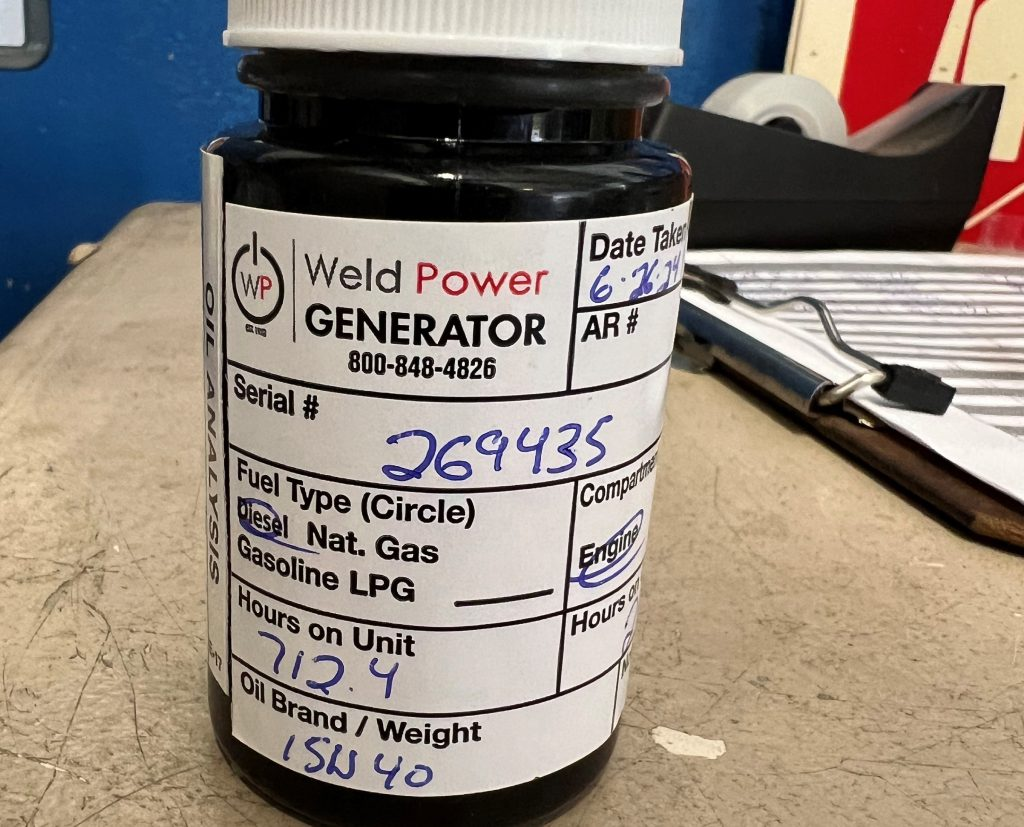
Importance of Oil Sampling & Testing
Quality oil is critical for any generator, providing lubrication, reducing friction, and preventing wear and tear on engine components. Regular oil sampling is a proactive measure that can identify potential issues before they escalate.
Detecting Contaminants: Oil analysis can reveal the presence of contaminants like dirt, metal particles, and water. These contaminants can indicate wear and tear or external ingress, which can lead to critical engine damage if not addressed.
Assessing Oil Condition: Over time, oil degrades and loses its effectiveness. Sampling helps determine the oil’s viscosity, acidity, and presence of oxidation, ensuring it’s still performing optimally.
Identifying Wear and Tear: By analyzing metal particles in the oil, it’s possible to identify which engine components may be experiencing excessive wear. This early warning allows for timely intervention and repair.
Optimizing Oil Change Intervals: Instead of relying on fixed schedules, oil analysis provides data-driven insights, allowing for more accurate determination of when oil changes are necessary, optimizing maintenance costs.
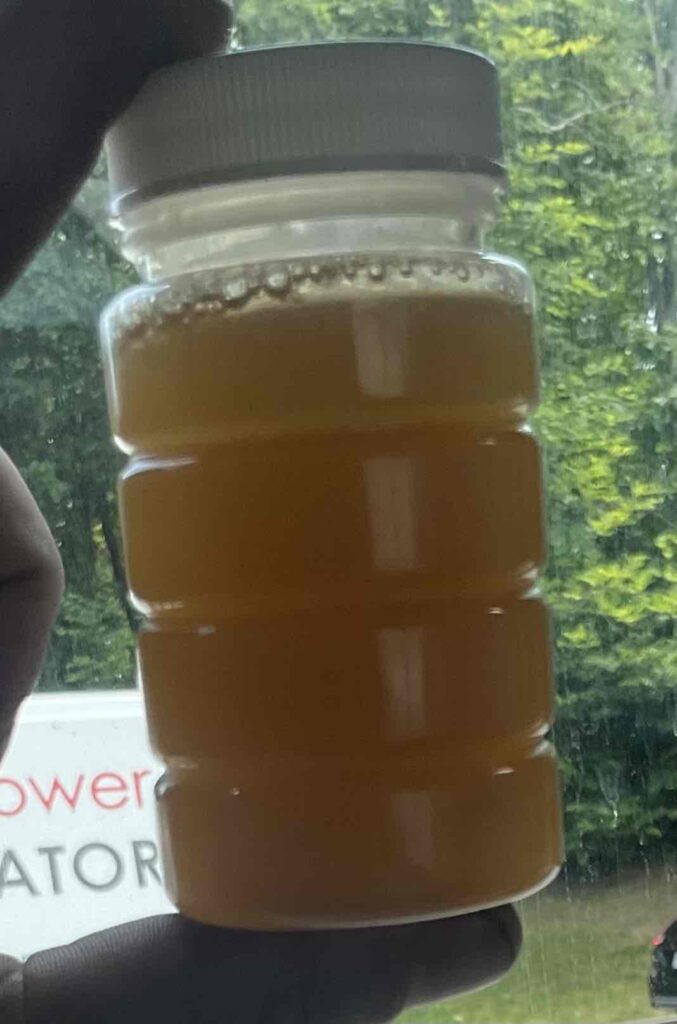
Importance of Coolant Sampling & Testing
Coolant plays a crucial role in regulating the engine’s temperature, preventing overheating, and protecting against corrosion. Regular coolant sampling is essential for maintaining the cooling system’s effectiveness.
Monitoring Coolant Quality: Coolant degrades over time, losing its ability to regulate temperature and prevent corrosion. Sampling ensures the coolant is still effective and within the desired chemical parameters.
Detecting Contaminants and Leaks: Coolant analysis can identify contaminants such as oil, fuel, and metal particles, which may indicate leaks or internal engine issues.
Preventing Corrosion: Coolant contains additives that protect against corrosion and cavitation. Regular sampling ensures these additives are at appropriate levels, safeguarding the engine’s internal components.
Ensuring Proper pH Levels: Maintaining the correct pH level in the coolant is vital for preventing corrosion and scaling. Sampling helps monitor and adjust pH levels as needed.
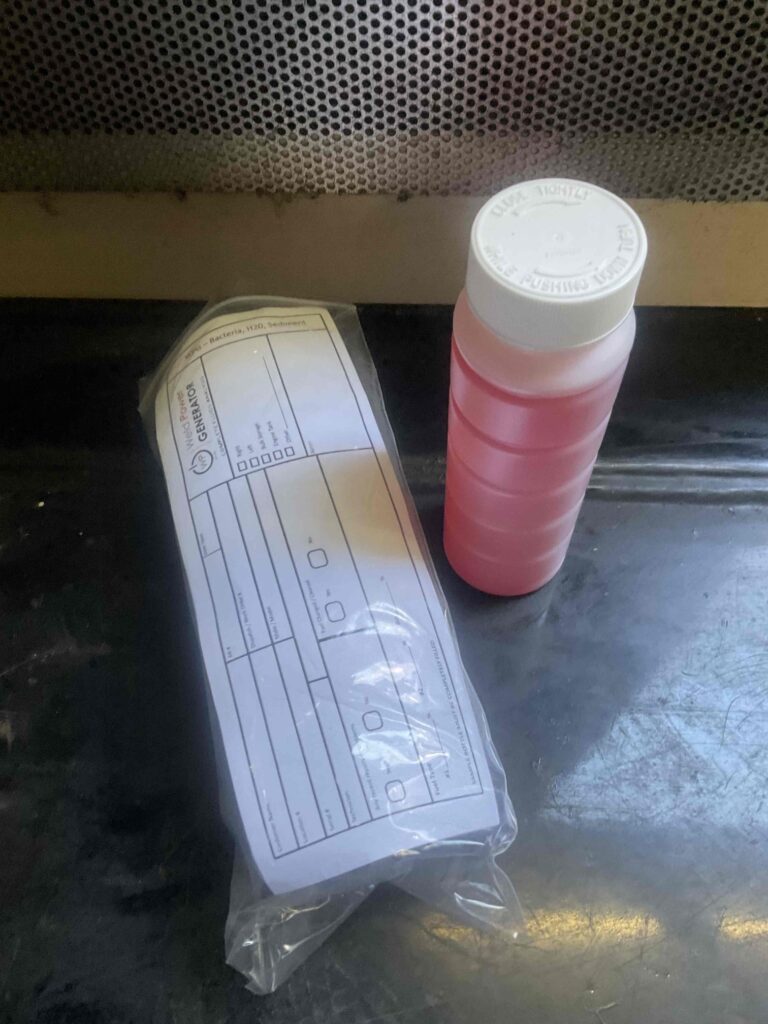
Importance of Diesel Fuel Sampling & Testing
One of the leading causes for generator failure is bad fuel. Fuel quality directly impacts the performance and reliability of a generator. Contaminated or degraded fuel can cause engine problems, reduced efficiency, and complete system failures. Recurring fuel sampling is key to preventing these issues.
Detecting Contaminants: Fuel sampling can identify water, microbial growth, dirt, and other contaminants that can clog filters and injectors, leading to engine performance issues.
Assessing Fuel Stability: Over time, fuel can degrade, forming gums and varnishes that impede engine performance. Sampling helps monitor fuel stability and identify when diesel fuel polishing or replacement is necessary.
Preventing Microbial Growth: In the presence of water, microbial growth can thrive in fuel systems, leading to blockages and corrosion. Regular sampling can detect microbial contamination early, allowing for timely treatment.
Ensuring Fuel Quality: High-quality fuel is essential for efficient combustion and optimal engine performance. Sampling ensures that the fuel meets the necessary quality standards and specifications.
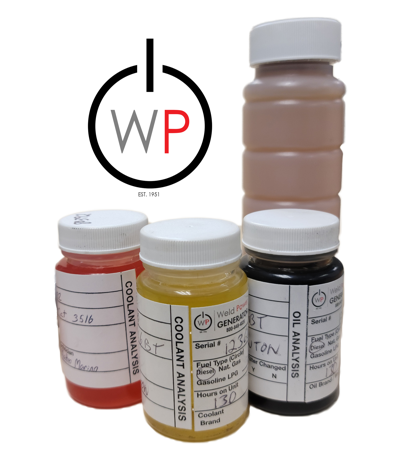
Conclusion
Incorporating oil, coolant, and fuel sampling into your generator preventative maintenance plan is not just a best practice—it’s a necessity. These proactive measures provide critical insights into the health and performance of your generator, allowing for timely intervention and preventing costly breakdowns. By regularly sampling and analyzing these fluids, you can:
- Extend the lifespan of your generator
- Optimize maintenance schedules and costs
- Ensure reliable and efficient operation
- Prevent unplanned downtime and associated risks
In an era where reliability and efficiency are paramount, investing in generator fluid sampling and testing is a smart strategy to keep your back-up power system running smoothly and effectively. By prioritizing these maintenance practices, you can ensure that your generator is always ready to deliver the power you need, when you need it.