The 13 Key Components of a Commercial Generator
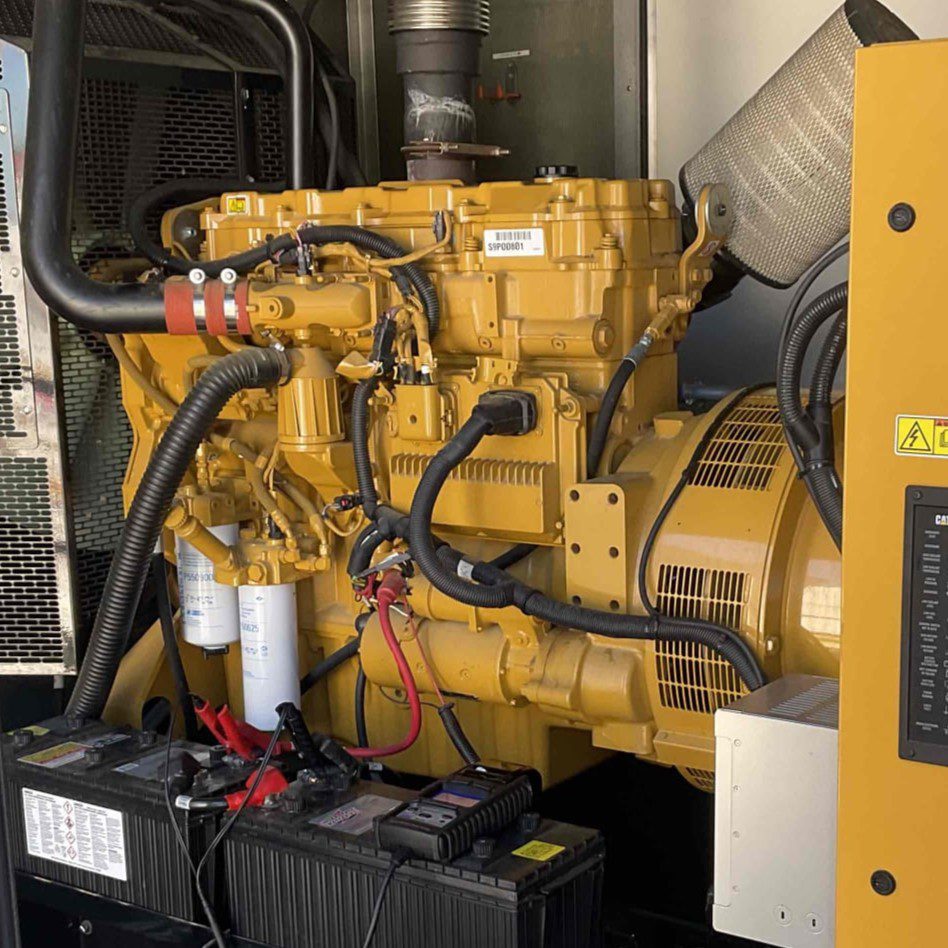
Although commercial generators come in many different makes and models, the key components remain the same. Each contributes to the generator’s overall functionality and reliability.
Table of Contents
Engine
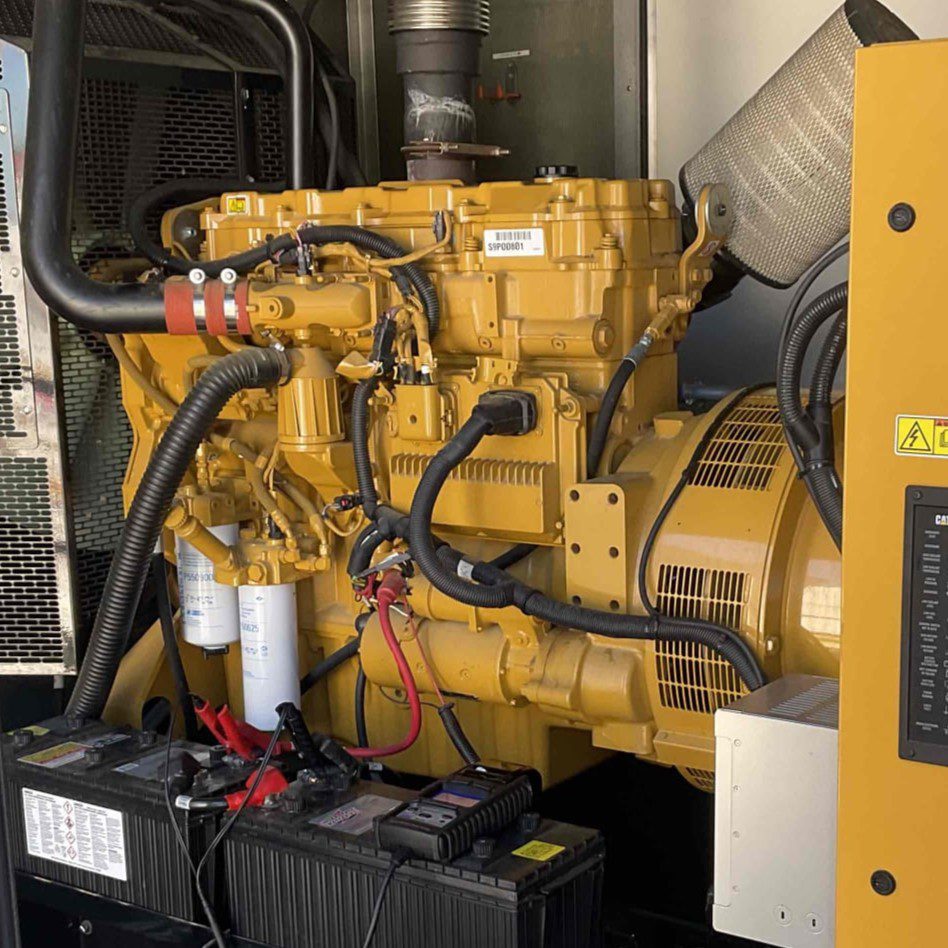
The engine of a commercial generator, similar to a vehicle’s engine, converts fuel into mechanical energy. While both use internal combustion to generate power, a generator engine is designed for continuous operation and consistent RPMs to produce steady electrical output, unlike a vehicle engine that operates at varying speeds.
Generator engines prioritize durability and efficiency under prolonged use, often running on diesel, natural gas, or propane. Regular generator maintenance is crucial for both, but generator engines demand stricter adherence to servicing schedules to ensure uninterrupted power supply, highlighting their role in critical backup and primary power applications.
Alternator (Generator Head)
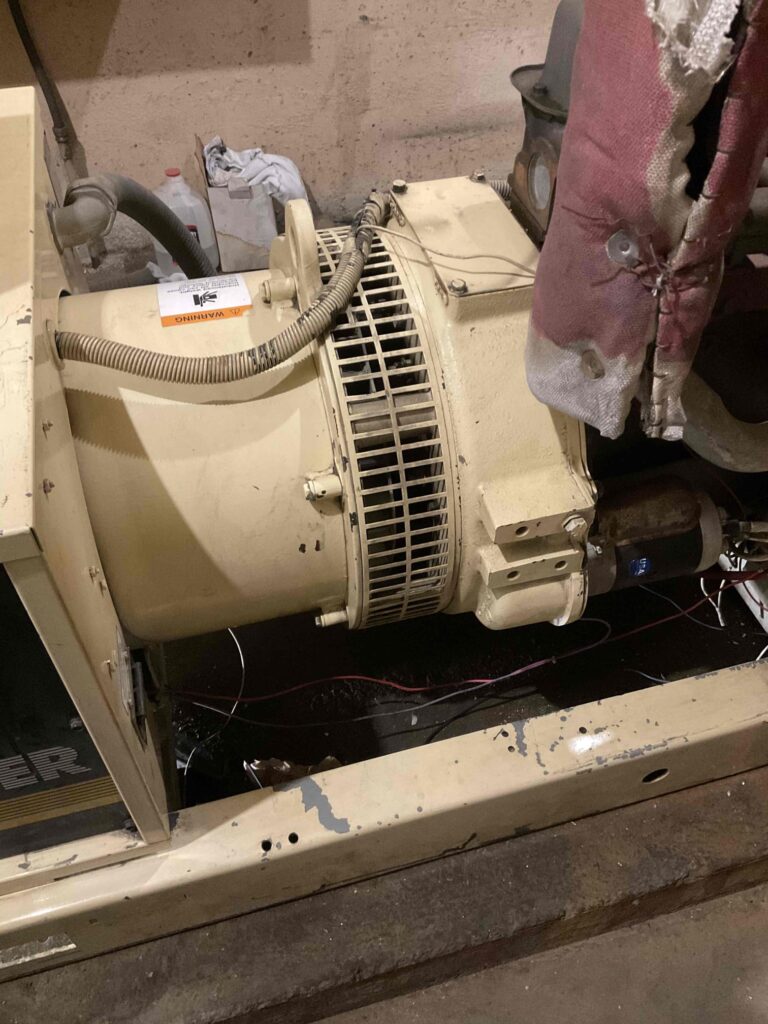
The alternator of a commercial generator converts mechanical energy from the engine into electrical energy. An alternator’s rotor is a rotating component typically composed of a shaft with a series of electromagnets or permanent magnets attached.
As the engine drives the rotor to spin within the alternator, these magnets create a rotating magnetic field. This magnetic field interacts with the alternator’s stator, a stationary component lined with conductive windings, inducing an alternating current (AC) in the windings. The rotor’s consistent rotation and magnetic field generation are essential for the alternator to produce a stable and reliable electrical output.
Unlike automotive alternators designed for intermittent use, commercial generator alternators are built for continuous, heavy-duty operation. Regular generator maintenance, including inspections and cleaning, is crucial to prevent overheating and wear, ensuring the alternator’s longevity and efficiency in providing uninterrupted electrical power.
Fuel System
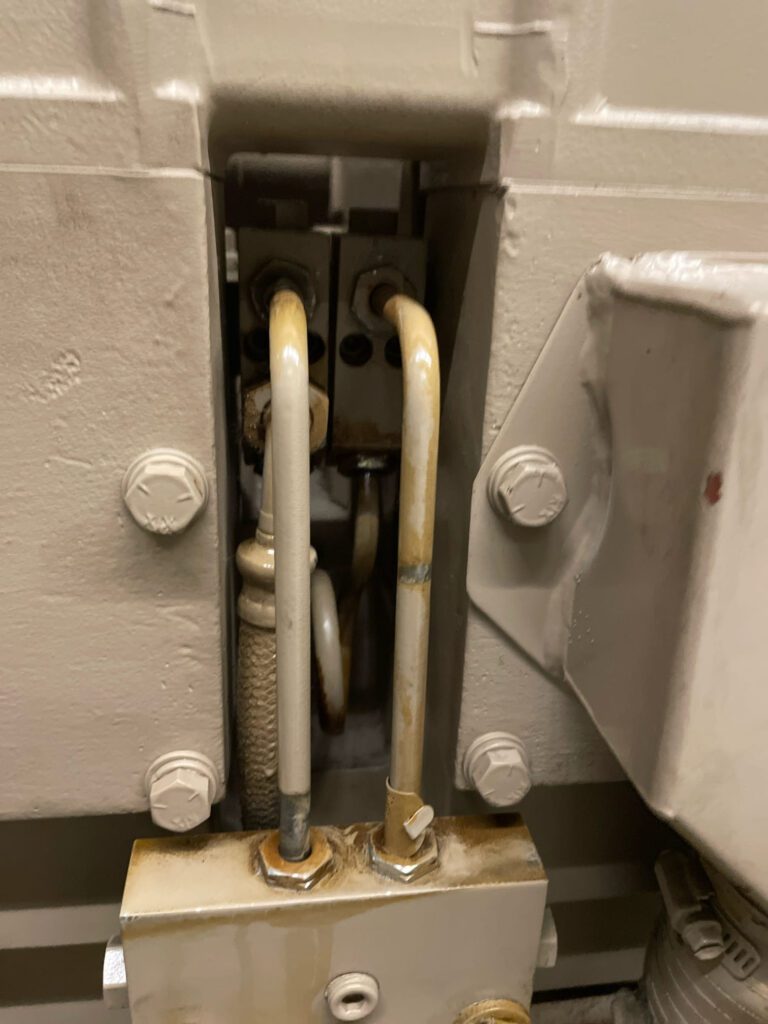
Although it is not technically a part of the generator itself, the fuel system begins at the fuel tank, which stores the diesel, natural gas, or propane needed to run the engine. From the tank, the fuel is moved through the fuel lines by the fuel pump. Before reaching the engine, the fuel typically passes through a filter to remove impurities.
The filtered fuel is then delivered to the injectors, which precisely inject it into the engine’s combustion chambers. This process ensures a steady, clean fuel supply for efficient engine operation and reliable power generation. Regular maintenance of these components is essential for optimal performance.
Voltage Regulator
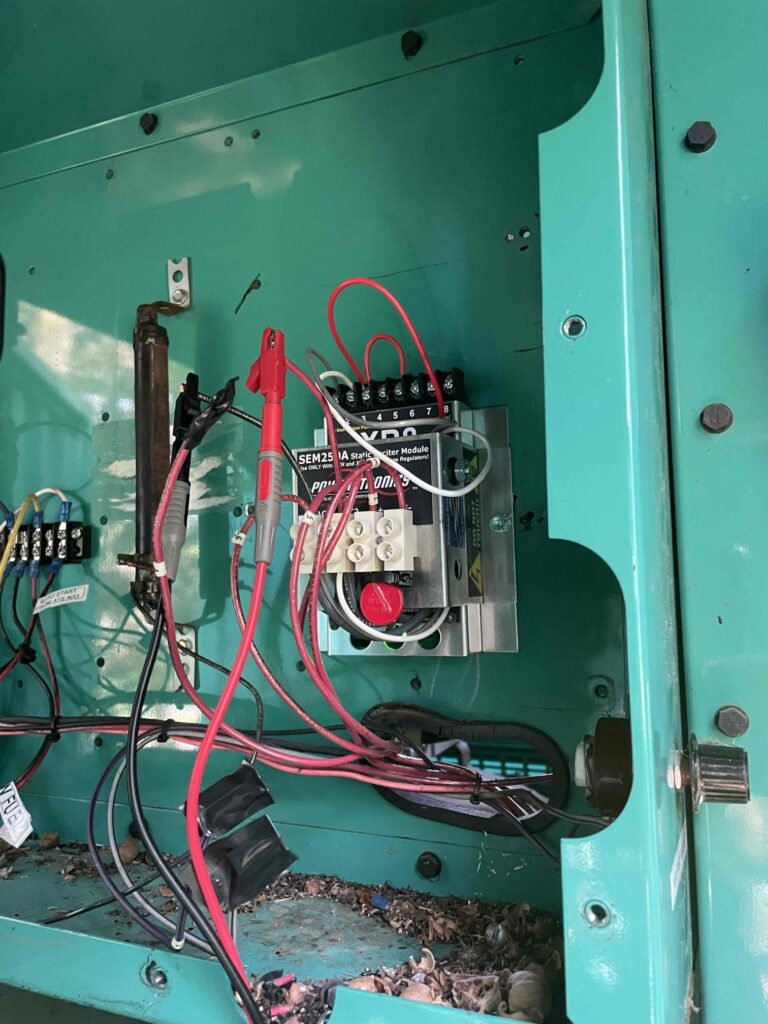
The voltage regulator of a commercial generator ensures a consistent and stable voltage output, which is vital for protecting the connected equipment. It monitors the generator’s output and adjusts the excitation to the alternator’s field windings, maintaining the desired voltage level. The voltage regulator ensures reliable power quality by compensating for load changes and preventing voltage fluctuations.
Regular maintenance prevents malfunctions and ensures continuous, optimal generator performance. This component is key to the generator’s ability to provide consistent, high-quality electrical power.
Cooling System
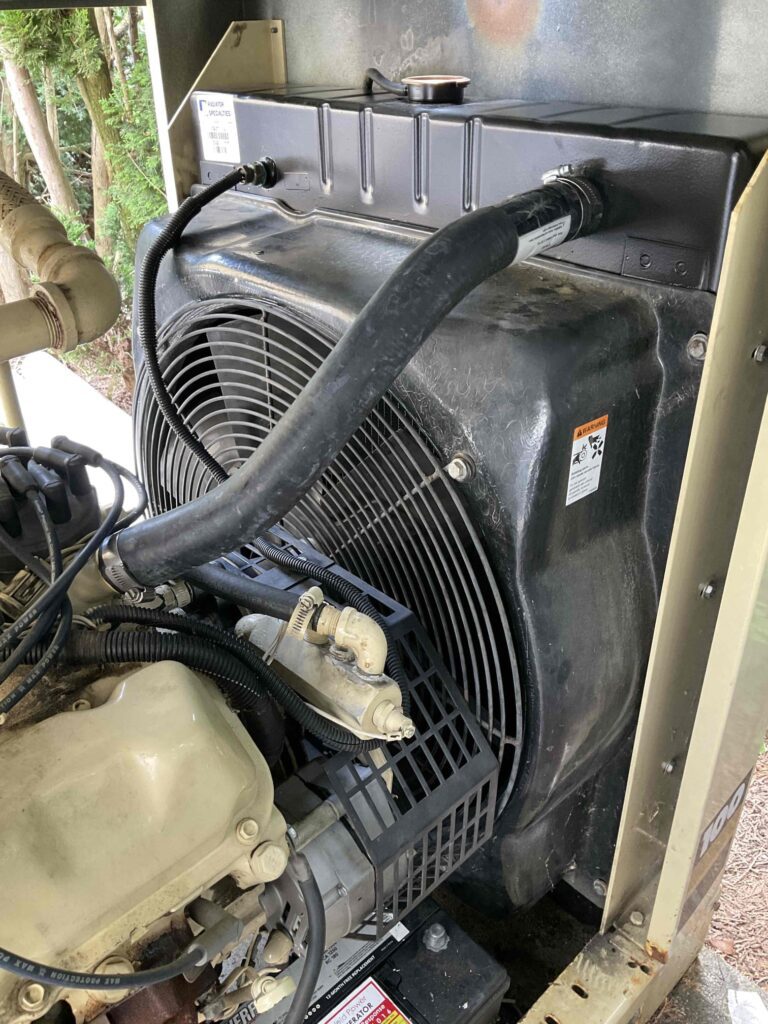
The cooling system of a commercial generator prevents overheating, ensuring optimal performance and longevity. Key components include the radiator, cooling fan, water pump, and thermostat. The radiator typically consists of a durable metal core with thin, parallel tubes through which coolant flows. Numerous thin fins surround these tubes.
A cooling fan pushes air between the fins to dissipate heat into the surrounding air. The water pump circulates coolant through the engine and radiator. The thermostat regulates coolant flow, maintaining the engine’s ideal operating temperature. Regular maintenance, such as checking coolant levels and inspecting the radiator and hoses, is essential to avoid overheating and ensure reliable operation. This system is critical for maintaining the generator’s efficiency and preventing costly damage due to excessive heat.
Exhaust System
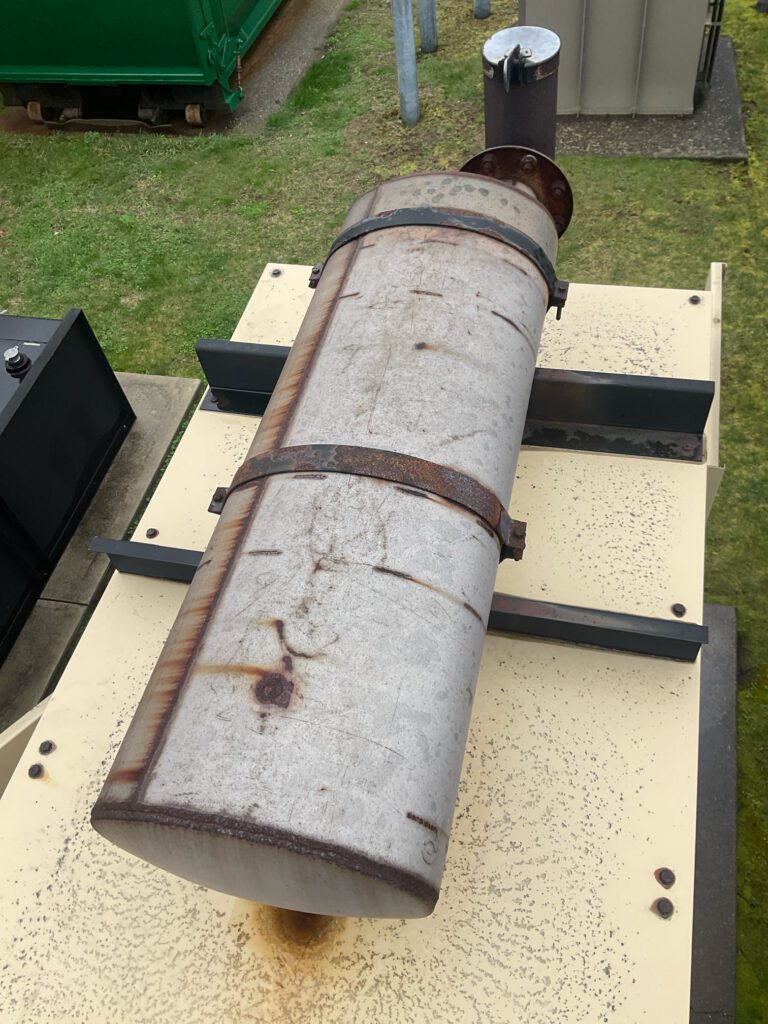
The exhaust system of a commercial generator safely channels combustion gases away from the engine. It typically includes a muffler to reduce noise and exhaust pipes that guide emissions away from the unit. This is especially important for indoor generators to prevent carbon monoxide buildup.
Proper ventilation and positioning are crucial for minimizing noise and maintaining air quality around the generator. Regular inspection and maintenance ensure efficient exhaust flow, preventing buildup and ensuring compliance with environmental regulations.
Lubrication System
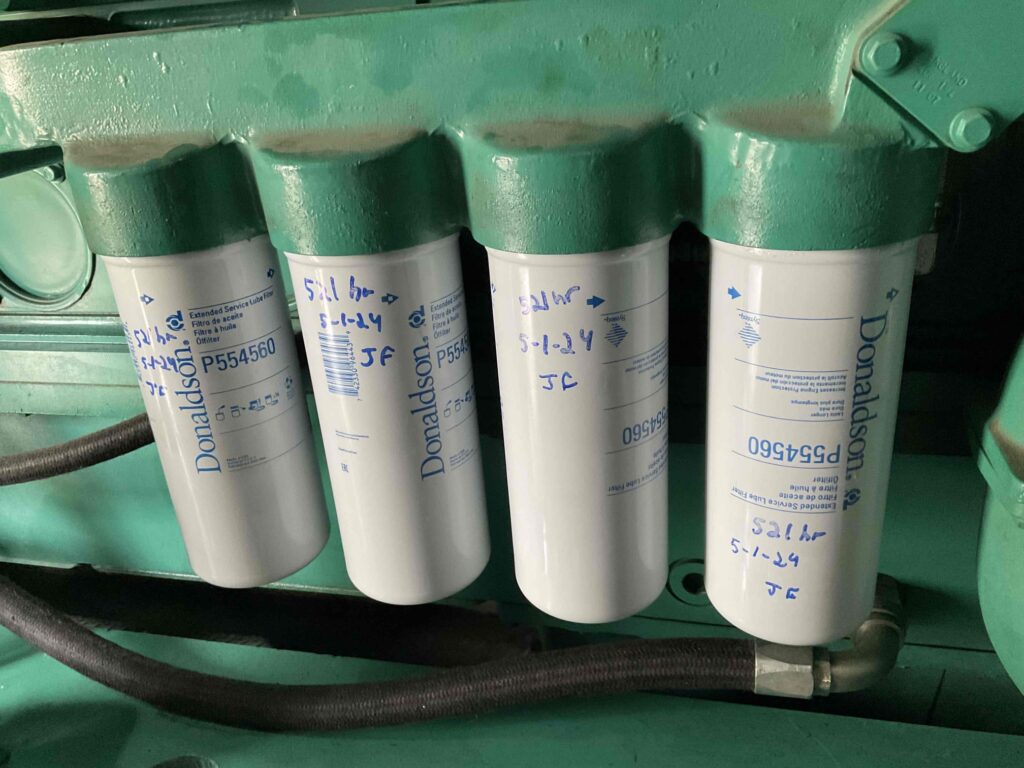
The lubrication system of a commercial generator ensures essential engine components remain properly lubricated for smooth operation and longevity. It includes an oil pump that circulates lubricant throughout the engine, ensuring parts such as bearings, pistons, and crankshaft are adequately lubricated to reduce friction and wear.
The system also features an oil filter to remove contaminants and maintain oil cleanliness. Regular oil changes and maintenance are crucial to preserve engine performance and reliability, preventing overheating and mechanical failures that could interrupt power supply.
Control Panel
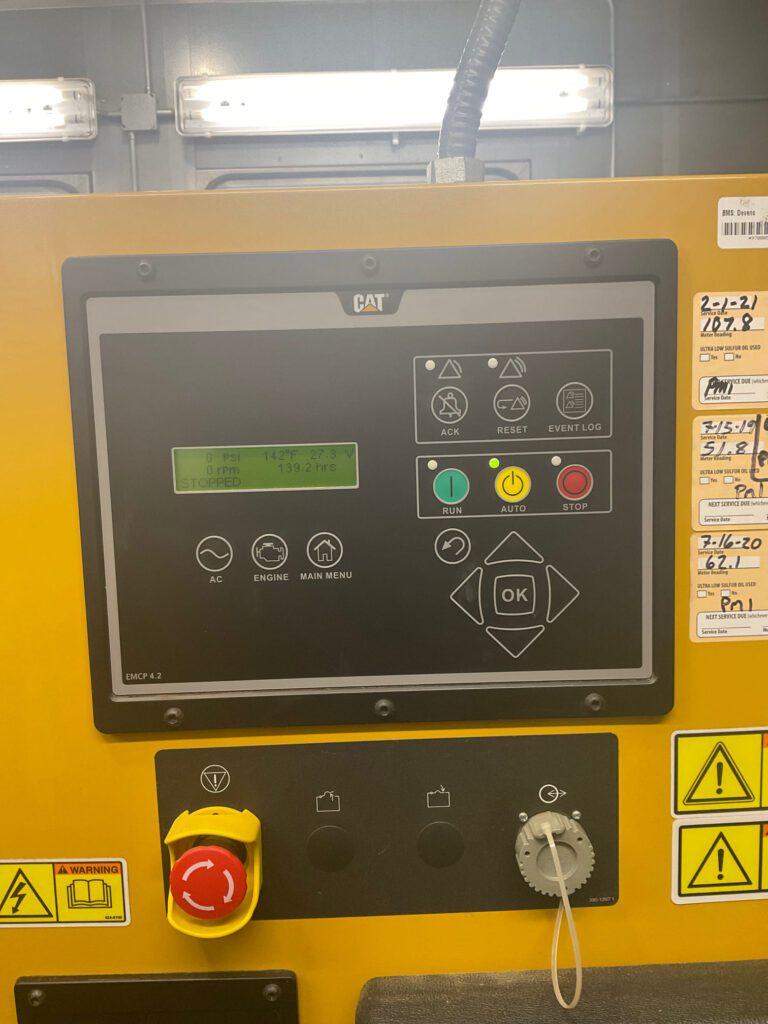
The control panel of a commercial generator serves as the command center, housing essential components for monitoring and managing the generator’s operation. It includes switches for starting and stopping the generator, indicators for voltage, current, frequency, and engine parameters, and controls for adjusting settings.
Some panels also feature digital displays or touchscreen interfaces for user convenience. The control panel enables operators to monitor performance, diagnose issues, and adjust operational parameters, ensuring efficient and reliable power supply to critical loads. Regular checks and familiarity with the control panel are vital for effective management and quick response during power disruptions.
Battery & Charger
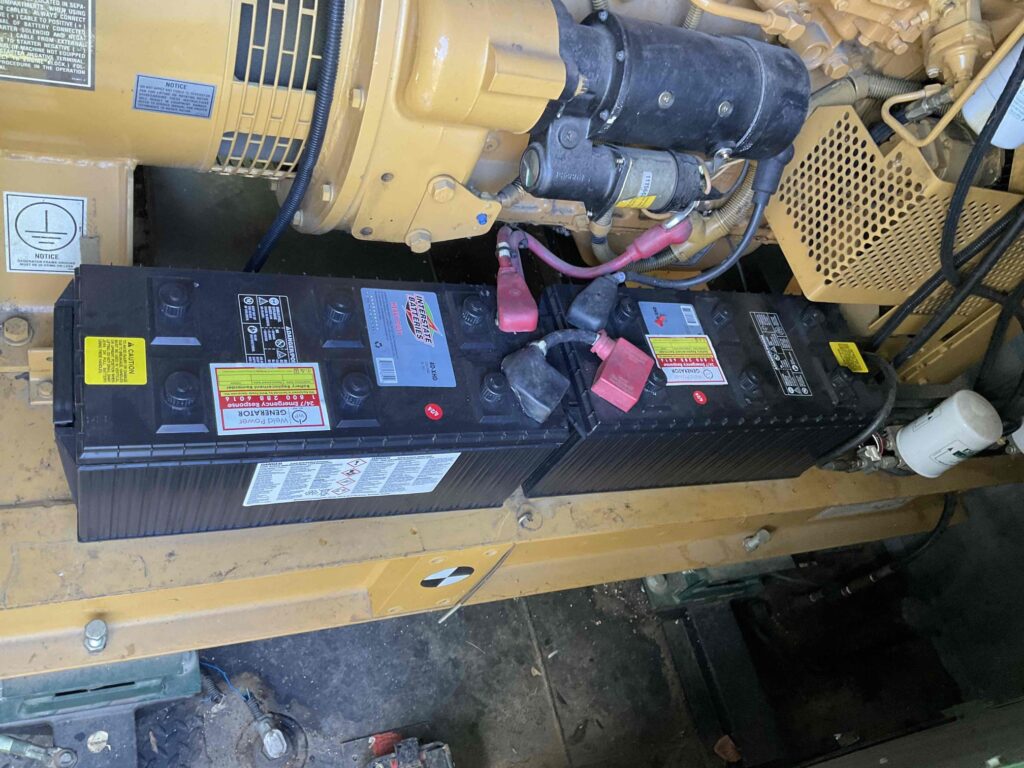
The battery charger of a commercial generator maintains the charge of the starting battery, ensuring reliable engine startup when needed. It automatically charges the battery during generator operation, using some generated electricity. This component is crucial for maintaining battery health and readiness, especially during extended periods of inactivity. Regular inspection and maintenance of the charger are essential to ensure optimal battery performance and to prevent starting failures during critical power outages.
Frame/Chassis
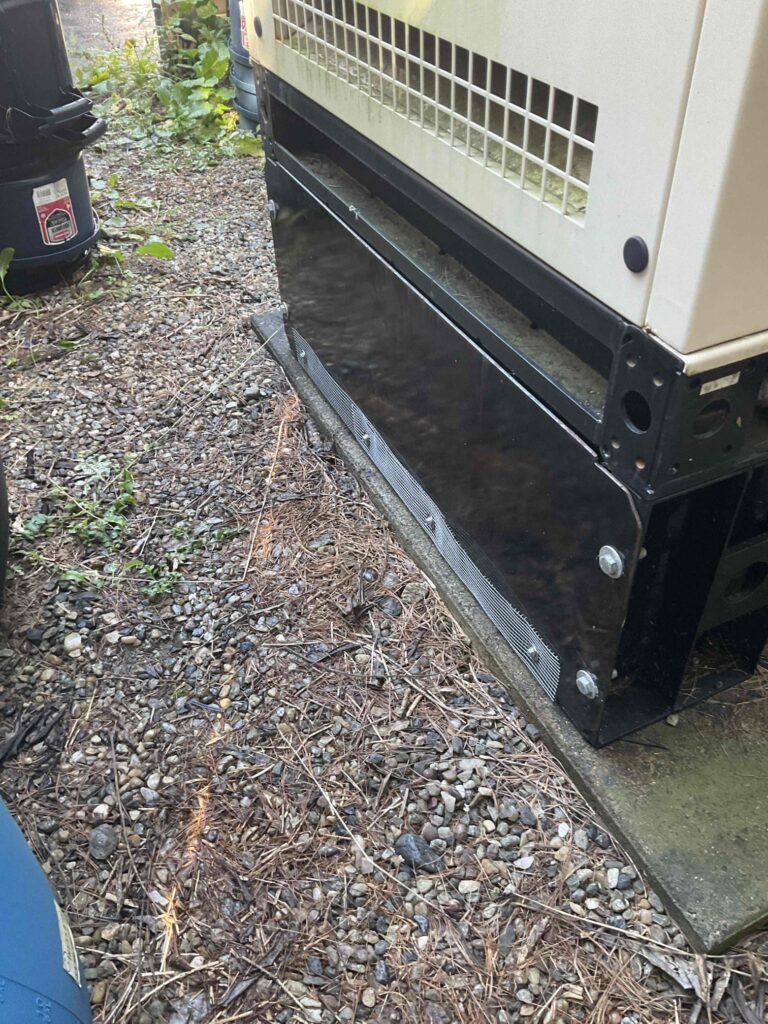
The frame and chassis of a commercial generator provide the structural support and stability needed to house and protect critical components. Typically constructed from materials like steel or aluminum, they are designed to withstand the rigors of transportation, installation, and continuous operation.
The chassis often includes mounting points for components such as the engine, alternator, fuel tank, and control panel, ensuring they remain securely positioned. Proper design and construction of the frame and chassis contribute to the generator’s reliability, longevity, and ability to function effectively in diverse environmental and operational settings.
Starter Motor
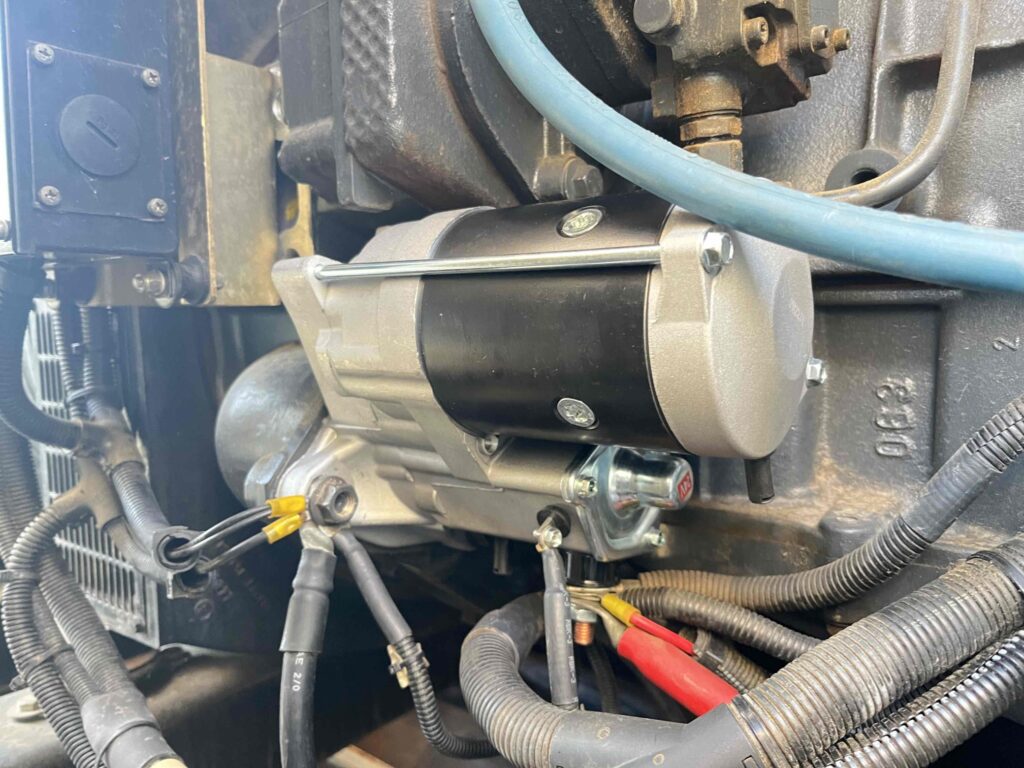
The starter motor of a commercial generator initiates engine startup by engaging with the engine’s flywheel or starting gear. It converts electrical energy from the battery into mechanical energy to crank the engine into motion. Essential for reliable generator operation during power outages, the starter motor ensures swift engine startup to restore electricity to critical loads.
Regular maintenance and testing of the starter motor are crucial to ensure it remains operational and responsive when needed, minimizing downtime and ensuring continuous power availability.
Governing System
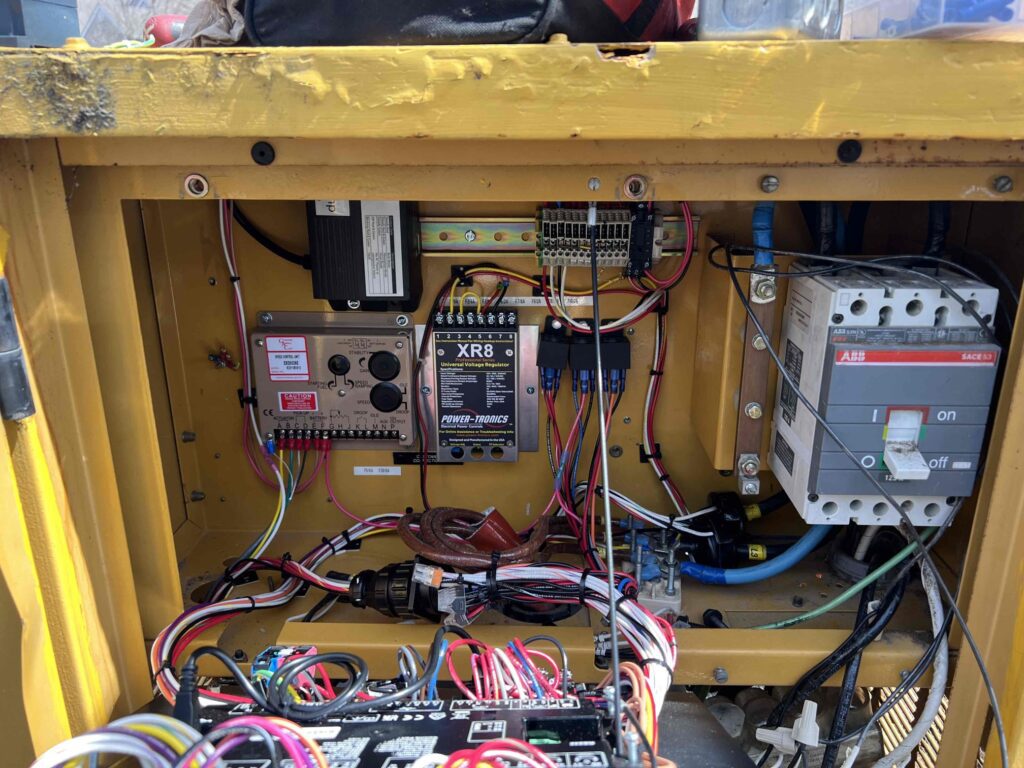
The governing system of a commercial generator regulates engine speed to maintain a consistent electrical output frequency. It controls fuel intake or ignition timing to adjust engine RPMs based on load demand, ensuring stable operation and preventing fluctuations in power quality.
This system is critical for maintaining the generator’s performance within acceptable limits and optimizing fuel efficiency. Regular calibration and maintenance of the governing system are essential to ensure accurate control of engine speed, reliability in power generation, and compliance with operational requirements.
Automatic Transfer Switch (ATS)
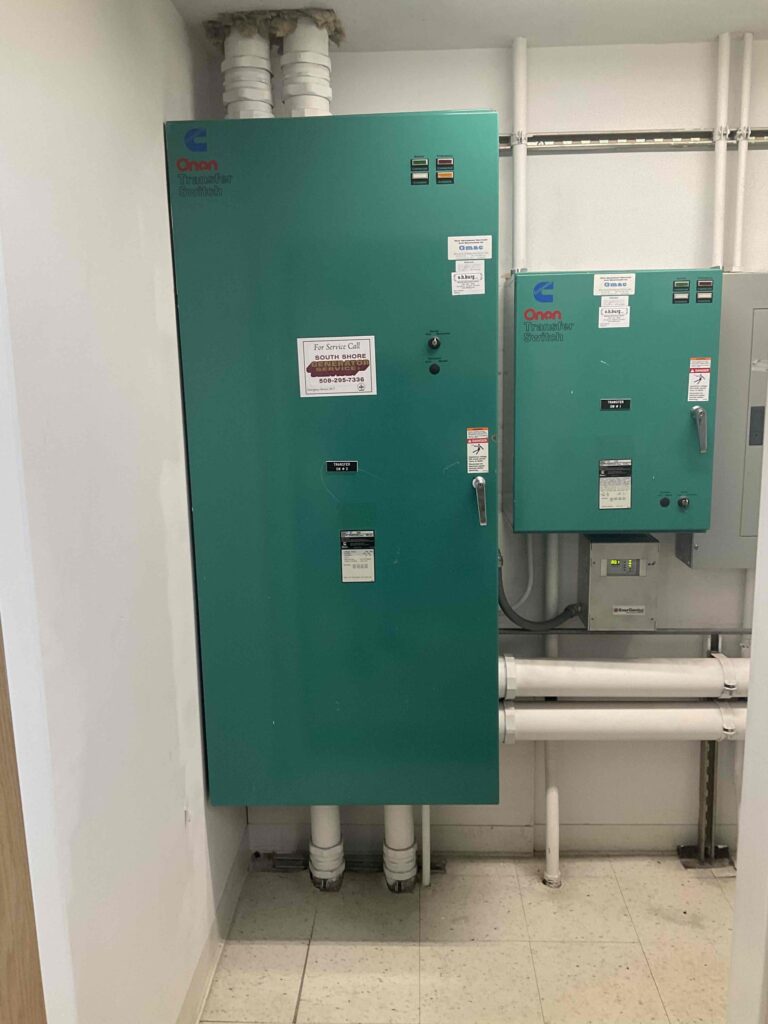
Although the Automatic Transfer Switch (ATS) is not part of the generator itself, it had to be mentioned due to its crucial role. The ATS automatically detects power outages and switches the electrical load from the main power source to the generator. It ensures uninterrupted power supply to critical systems and devices during outages, reducing downtime.
ATS units are equipped with sensors to detect utility power restoration, seamlessly transferring the load and shutting down the generator. Proper installation, ATS maintenance, and testing ensure reliable operation. ATS units ensure continuous power availability for businesses, facilities, and sensitive operations.